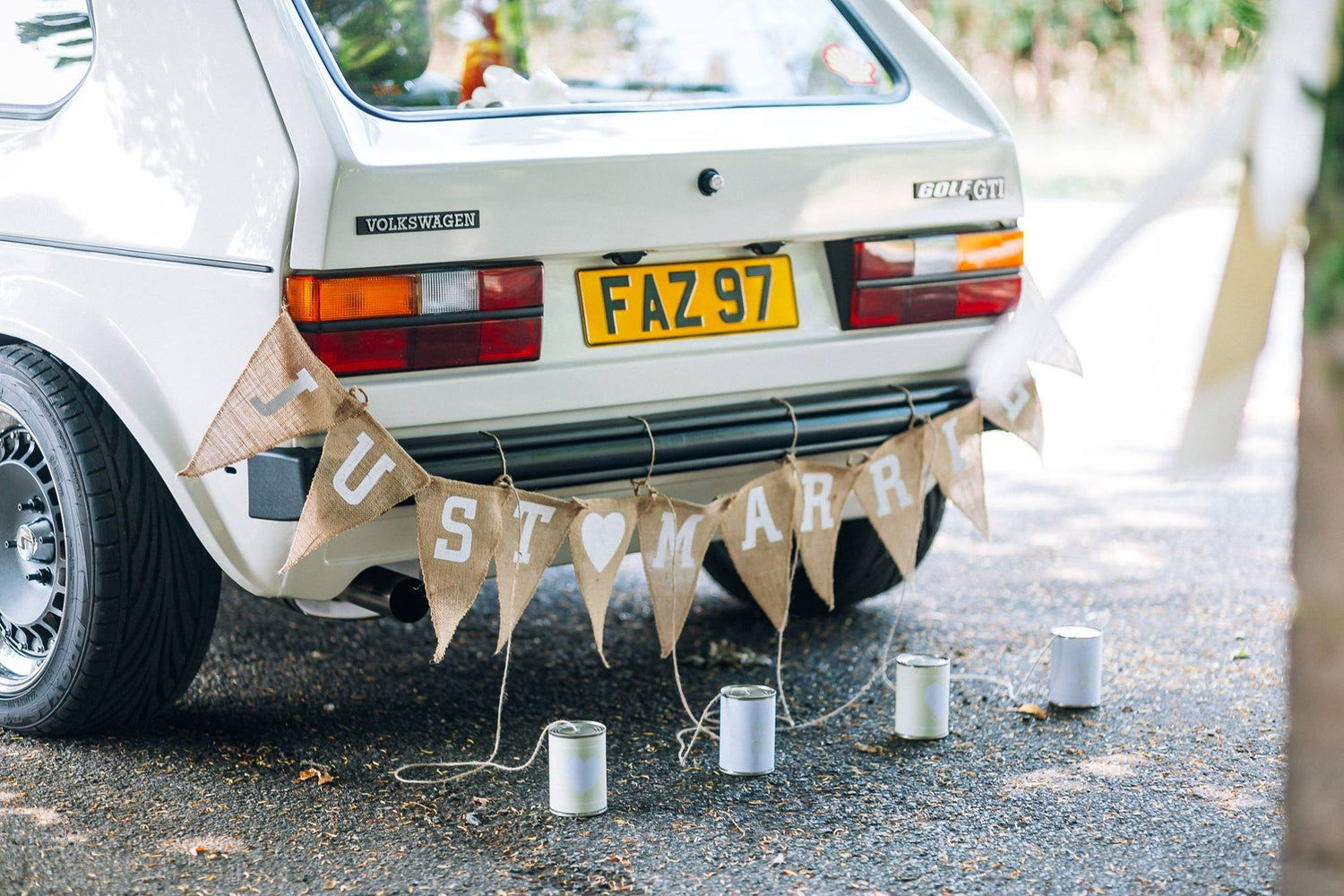
This car was built by us a couple of years ago now but it is one that we loved being involved in, not only because of the way the car turned out but also because of the sentimental value to its owner, Matthew Farrell. This was a restoration which started as a home build before coming to us at Motion, meaning that some parts of the process aren’t documented as well as we’d like and if we’re honest, we could talk all day about every little detail but nevertheless, it’s some story.
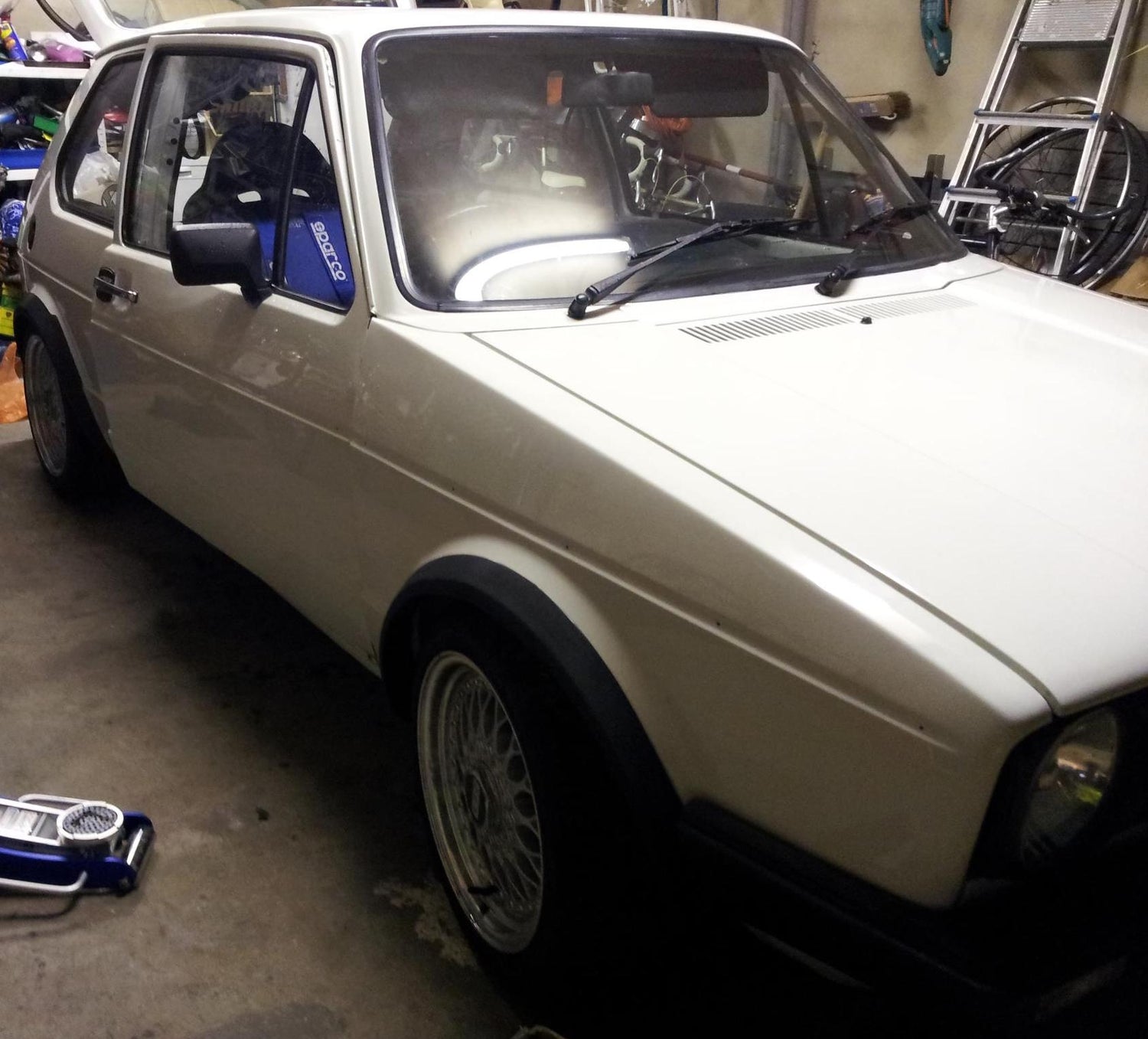
The Car
Matt is a school friend of Jake’s. Both of them have a real bug for the VW brand (see what we did there?) and scene. The car is a 1983 VW Golf GTi which Matt bought as an unfinished project in 2011; already ABF converted, tatty and poorly put together but on the face of it, a reasonably solid base to work from (or so it seemed).
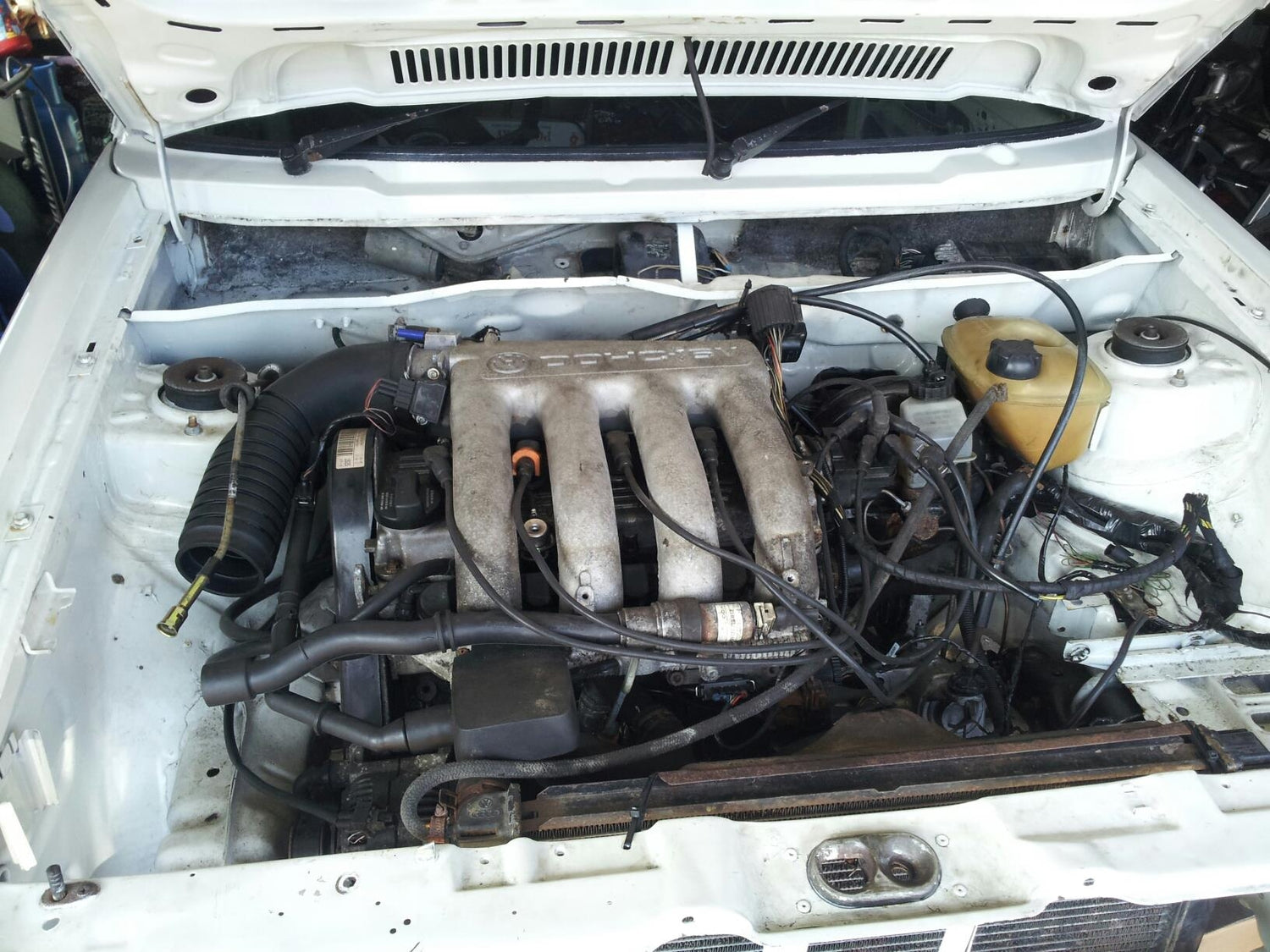
Matt works as an engineer at Bentley. He isn’t shy with a set of spanners and had the intention of a light restoration but mainly just to finish the project off. Once the car was back at Matt’s house, his first job was to get it running, have a look around it and make a list. You can imagine the excitement as he connected the battery, cranked for oil pressure and re-connected the coil before turning the key. It fired up, spat a couple of litres of oil out of the exhaust and then the fuel lines fell off. Not a great start.

It would seem that an engine build was now top of the ever growing list. Removing bumpers and trim led to bodywork coming away with it, jacking points going through the sills and so on. This was going to be a much bigger job than anticipated and something that – looking back – goes to show why we all seem to find some inner drive and desire in the face of adversity when it comes to projects, especially cars.
The Strip Down and Preparation
The car was stripped to a bare shell and then acid dipped. Dipping a shell is the easiest and most thorough way of stripping back all rust, underseal and 35 years of grime to reveal the true extent of the work needed to get the Golf structurally sound and lay the foundations of what was to come. This was the first time (but not the last) that Matt considered throwing in the towel and getting a new shell. The dipping process had unveiled a very weathered Mk1 Golf.
After much deliberation, the decision to continue with this shell was made. Matt spent hours cutting away panels and rotten sections of shell, including a replacement roof skin to delete the factory sun roof. Luckily, VW Heritage for the most part and some German Ebay finds meant that almost every single panel was sourced meaning that there is no ‘patches’ in this car. Each rotten panel was replaced with new.
Protection
Once a car has been acid dipped and all metalwork repaired or replaced, it is then re-dipped in preparation for the next process. Before the shell is ready to go to paint there is another process which it must go through to protect it from the elements in future: E-coating. The E-Coat Process (or KTL) is used by every major automotive manufacturer in the world. Over 95% of the worlds motor vehicles are primer protected with the cathodic electrocoat process. There is no better way to add front line corrosion protection coating to a complex assembly like a vehicle bodyshell. Over 300 million vehicles have been coated with this process to date.
Shells and components are immersed in an 11 stage cleaning and pre-treatment process that deposits a corrosion resistant layer of Zn/Mn/Ni Phosphate. They are then immersed into the PPG Electrophoretic Epoxy Primer which is electrically bonded to the surface before being cured in an oven at 185ºC for 45 minutes leaving an impermeable, durable primer finish. Comprende?
Paint
Now, with the shell ready for paint and fully protected against corrosion in future, the car went to the body shop for a coat of VW Cashmere white inside and out. The original colour of the car was Alpine white so it’s not a huge change and remains a VW colour for the purists.
If you’ve ever gone through this process or had a car painted before, you’ll know the excitement that runs through your veins as you make your way over to the paint shop to collect it. Well this time, Matt’s joy quickly turned to disappointment. Looking around the car showed poor prep and paint finish, picking out a handful of things needing attention straight away. After a mildly heated discussion, it was agreed that the car would be re-prepped and painted a second time to ensure that the finish was nothing short of perfect.
Fast forward a couple of weeks and the car was ready again and Matt made his way over to be greeted again with a car that just was not up to scratch. The paint finish was much better this time around but there were still issues with the roof gutters not being flat or even, runs in the edges of panels – you get the idea. At this point, Matt was understandably devastated and ready to accept the sub-standard of finish and just get the car built, which is where we were asked to step in and get involved with the project!
Our input at this stage of the build was to provide full reassurance that we could help to get the car built to the best possible standard and also to give Matt a build plan to follow. The car deserved the best at this stage and we wanted to ensure that any penny spent was A) spent wisely and B) spent in the right places. We decided together that the car needed to be painted for a third time but using a body shop we had full confidence in achieving the level of finish we were looking for. Loaded onto a transporter, the shell was delivered to Russ at Cheadle Body Shop.
Assembly
The car came back exactly how it should have done the first time; paint like glass and not a blemish or poor panel fit in sight. We spoke with Matt about how to proceed at this stage and decided that he would take the car with him to start with the assembly process of getting the car rolling and we would take the engine and gearbox. The plan with the engine was to build something reliable, clean and usable but with the character that a MK1 deserves. The spec of the engine and gearbox are included in the full spec sheet at the bottom of the page.
Over the next couple of months the car came together in the workshop and was ready to go to SpeedFab for a custom manifold and exhaust. They made a fantastic job. The fit and workmanship is top notch and it really looks at home in the clean engine bay of the Golf.
A couple of months passed by, we had the engine/gearbox built and Matt had the car rolling. The car was delivered to us to get cracking with the assembly process of the drivetrain, fuel system, braking system and get the car ready for a wiring loom. Although the car originally had the ABF fitted, we started again with every part of the install and the addition of the throttle bodies meant we were a little nervous to see whether the bonnet would close with the trumpet length we had chosen. It needed a little fettle but it did!
Over the next couple of months the car came together in the workshop and was ready to go to SpeedFab for a custom manifold and exhaust. They made a fantastic job. The fit and workmanship is top notch and it really looks at home in the clean engine bay of the Golf.
The car then went for its complete wiring loom install. As you can imagine the original wiring loom was in a real mess from the botched conversion and was a fire waiting to happen. After a full re-wire, the car returned to us for the first fire up, check of all systems and final preparation for mapping including the first time in nearly 8 years that this car had turned a wheel under its own power. Things really start to come together at this stage and it’s amazing to see the vision you have at the start of a project come to life.
The interior and all exterior trim could now be finished with the wiring loom and all systems checks complete. This is one area that Matt had covered from the start, he used his skills as a trimmer at Bentley and refurbished the original GTi seats with new foam and trimmed them in some of the finest perforated leather and red stitching. The craftsmanship is incredible and keeps the character of the car alive whilst being individual enough to stand out.
There was never really a planned ‘finish’ date for the build, especially with the various obstacles that Matt encountered along the way. It was always the plan to make the car the best it possibly could be, however, with his wedding date set for July 2018, Matt wanted to use the car to carry himself and his new bride from the church (awwwwww). With that in mind, we booked the car in for its mapping session with Chris at EFI parts for early 2018.
The car made solid numbers on the dyno at 193hp and with a lovely torque curve, it was ready for MOT and its first outing in March; well in time to sort any teething issues out before the wedding. As expected, the car has been faultless since the build. Matt has racked up around 2000 miles and a couple of awards including a ‘Best at Show’ which is a testament to the time, effort and pride that went into this car.
Out of all the cars we have built, this one was particularly special because of the journey that the car has been through. As Matt is a good friend of Jake we were aware of all the issues leading upto the point we were asked to step in and so seeing the finished article used as his wedding car was a really nice touch and an absolute pleasure to be a part of the process. Luckily his marriage hasn’t had the same roller coaster of emotions either!
Thanks for reading, until next time…
Brief Spec list
2.0 16V ABF Engine
JE pistons 1mm oversize, 11.3:1
Cat Cams forged rods
Cat Cams and Vernier pulley
Balanced rotating assembly
AT Power throttle bodies
Speed Fab custom spec manifold and exhaust
OMEX 600 management
Epytech engine mounts
Custom sized Pro Alloy radiator
02A Gearbox
Complete bearing and seal rebuild
Quaife ATB differential
CAE shifter and cables
Fueling
New stock GTi tank
Bosch 044 fuel pump
Aeromotive Fuel pressure regulator
Hardline under car and Teflon braided line in engine bay
Suspension
AP Coilovers with camber/caster top mounts
Powerflex bushes throughout
MK2 front hubs
Brakes
Wilwood pedal box
Wilwood 4 piston front calipers
MK4 Golf rear disc conversion
Braided lines throughout
Interior
Refurbished and retrimmed GTi seats
Momo steering wheel
New carpets, trim and sound deadening
Red seat belts